
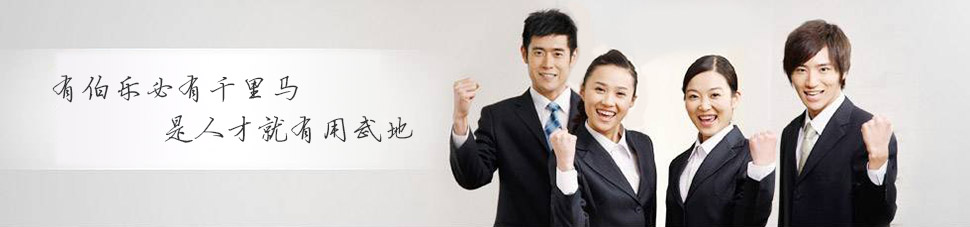
SQE Supervisor(Automotive)
更新日期:2019-09-19- 工作經(jīng)驗(yàn):
- 無要求
- 最低學(xué)歷:
- 本科
- 招聘人數(shù):
- 1
- 語言要求:
- 無
- 工作性質(zhì):
- 無
- 薪資范圍:
- 20-30萬/年
- 職位類別:
- 工作地點(diǎn):
- 廣州市
Requirements:
1.Familiar with mechanical parts,such as plastic,metal,etc..know about electronic component,
2.Automotive work experience,familiar with the quality standard of automotive industry,
3.Good oral English,
4.Anti-pressure ability,passionate,aggresive,
5.Good leadership,good communicate skill.
SUMMARY
The Supplier Quality Engineering Manager administrates and leads a group of technical professionals comprised of Supplier Quality Engineers, Component Specialists, Component Engineers and Receiving Inspection. The Supplier Quality Engineering group is a technical resource for Jabil suppliers and component issues, is responsible to drive manufacturing supplier related issues, periodic Supplier Evaluations, AMPL (Approved Manufacturer Part List) creation and maintenance, and Receiving Inspection management.
ESSENTIAL DUTIES AND RESPONSIBILITIES include the following. Other duties may be assigned.
LEADERSHIP AND MANAGEMENT RESPONSIBILITIES
Recruitment and Retention:
· Recruit and interview Supplier Quality Engineering Staff.
· Communicate criteria to recruiters for Supplier Quality Engineering Staff position candidates.
· Monitor team member turnover; identify key factors that can be improved; make improvements.
Employee and Team Development:
· Identify individual and team strengths and development needs on an ongoing basis.
· Create and/or validate training curriculum in area of responsibility.
· Coach and mentor Supplier Quality Engineering staff to deliver excellence to every internal and external customer.
· Create and manage succession plans for Materials function.
Performance Management:
· Establish clear measurable goals and objectives by which to determine individual and team results (i.e. operational metrics, results against project timelines, training documentation, attendance records, knowledge of operational roles and responsibilities, personal development goals).
· Solicit ongoing feedback from Workcell Manager (WCM), Business Unit Manager (BUM), peers and team member on team member’s contribution to the Workcell team. Provide ongoing coaching and counseling to team member based on feedback.
· Express pride in staff and encourage them to feel good about their accomplishments.
· Perform team member evaluations professionally and on time.
· Drive individuals and the team to continuously improve in key operational metrics and the achievement of the organizational goals.
· Coordinate team activities and insure focus during times of crisis.
· Ensure recognition and rewards are managed fairly and consistently in area of responsibility.
Communication:
· Provide weekly communication forum for the exchange of ideas and information with the department.
· Organize verbal and written ideas clearly and use an appropriate business style.
· Ask questions; encourage input from staff.
· Assess communication style of individual team members and adapt own communication style accordingly.
FUNCTIONAL MANAGEMENT RESPONSIBILITIES
Business Strategy and Direction:
· Know and understand the campus strategic directions.
· Define, develop and implement a Supplier Quality Engineering strategy, which contributes to the campus strategic directions.
· Develop an understanding of the Workcell business strategy as it pertains to Supplier Quality Engineering.
· Provide regular updates to BUM, WCM, and Materials Manager on the execution of the strategy.
Cost Management:
· Identify creative ways to reduce cost by streamlining processes and systems (i.e. modification of responsibilities or consolidation of tasks, elimination of non-value-added processes, or complete re-engineering of processes and systems).
· Utilize tools to monitor departmental cost and cost trends, striving continuously to improve value.
· Provide feedback to peers (BUM, WCM, and Functional Managers) on cost and cost trends.
· Forecast Development and Accuracy:
· Prepare timely forecasts for the department.
· Compare forward forecast results to historical actual results for trend assessment and analysis.
· TECHNICAL MANAGEMENT RESPONSIBILITIES
· Ensure that critical supplier issues affecting manufacturing operations are resolved in a timely manner, and corrective actions implemented properly.
· Ensure that Receiving Inspection, RTV, SCAR database, MRB, and customer returns related to supplier issues data is captured correctly and available to users.
· Ensure ongoing site supplier evaluation is performed, supplier performance reported internally, to the supplier and to the customer if applicable.
· Enable technology for creation and maintenance of company AMPL within customer established guidelines.
· Establish with Supplier Quality Engineers the appropriate Inspection Plans and Inspection Methods for Receiving Inspection function.
· Provide technical support to SCM personnel on supplier evaluation and selection.
· Support customer business needs using standard process where possible and customized solution where necessary.
· Adhere to safety and health rules and regulations associated with this position and as directed by supervisor.
· Comply and follow all procedures within the company security policy.
公司網(wǎng)址:http://jzbilweb.corp.jabil.org/
公司地址:廣州市經(jīng)濟(jì)技術(shù)開發(fā)區(qū)駿成路128號(hào)
捷普電子(廣州)有限公司成立于2011年,美商獨(dú)資進(jìn)料加工企業(yè),投資總額2.3億美元。廣東省、廣州市政府重點(diǎn)扶持發(fā)展的高新技術(shù)產(chǎn)業(yè)企業(yè)。公司2003年2月底正式投產(chǎn),占地面積約15萬平方米,建筑面積約19.6萬平方米,廠房面積約33,300平方米,員工約10000名。自建廠以來,公司業(yè)績(jī)發(fā)展良好,2007年進(jìn)出口金額18.63億美元;2010年進(jìn)出口金額增至32.18億美元,創(chuàng)歷史新高!公司多次榮獲捷普集團(tuán)、客戶、廣東省及廣州市政府、海關(guān)、商檢等部門嘉獎(jiǎng);如海關(guān)總署“2006年度進(jìn)出口紅名單企業(yè)”、中國進(jìn)出口200強(qiáng)企業(yè)、廣州出口第二大企業(yè)、黃埔海關(guān)AA類企業(yè)、廣州出入境檢驗(yàn)檢疫局評(píng)定的“一類企業(yè)”、廣州開發(fā)區(qū)優(yōu)秀職工之家等。我司主要產(chǎn)品系列有汽車電子產(chǎn)品、計(jì)算機(jī)外圍設(shè)備、無繩電話機(jī)組件、通信產(chǎn)品、網(wǎng)絡(luò)產(chǎn)品、打印機(jī)及其電路板組件、不間斷電源裝置、消費(fèi)電子產(chǎn)品、電子儀器、家用娛樂電子產(chǎn)品等。我司倡導(dǎo)“關(guān)注員工、關(guān)注客戶、有效的質(zhì)量控制”的企業(yè)文化,注重以人為本等人性化的企業(yè)文化氛圍建設(shè)。公司一貫遵循“遵紀(jì)守法”“誠信為本”的經(jīng)營原則,從而業(yè)績(jī)發(fā)展態(tài)勢(shì)良好。
捷普電子(廣州)有限公司
- 企業(yè)性質(zhì): 三資企業(yè)
- 業(yè)務(wù)范圍: KPO
- 所屬行業(yè):電子技術(shù)/半導(dǎo)體/集成電路
- 公司地址:廣州市經(jīng)濟(jì)技術(shù)開發(fā)區(qū)駿成路128號(hào)
該公司其他職位
更多>>- C&B Assistant / 薪酬福利助理 / 人力資源助理2014-08-29
- 生產(chǎn)組長2014-08-29
- Assistant Buyer-急招2014-08-29
- 生產(chǎn)線管理培訓(xùn)生 (2014應(yīng)屆畢業(yè)生)2014-08-29
- 生產(chǎn)管理培訓(xùn)生2014-08-29
最近瀏覽的職位
- SQE Supervisor(Automotive)2019-09-19